High Over The Hill on Sheep Pond Dr., Brewster, MA
One of our current projects for Winter of 2012, this home was purchased by the Driscoll family a few years ago. Renovations were done to the basement back when purchased, and we have been hired to renovate the entire main floor as well as include two additions to the existing home which was built in 1964. I’m not sure, maybe we just get lucky, but again we’re working for an awesome family with tastes that perfectly align with what we love to do. Plans had been drawn by an architect years ago in anticipation of this renovation, but after studying them a bit, we had to redraw them and make a few changes before we could begin. A great, creative, challenging project - the toughest aspect being that every utility that enters the home runs directly through where the master-bedroom/master-closet/master-bathroom addition and foundation will be placed, and all utilities have to be relocated to another part of the home while the family maintains residence undisturbed in the apartment below. But while challenging, it’s also super rewarding because there’s lots of wood interior finishes - which we love - and brick, and glass, and tons of sunshine, and a massive pond, and stone, and great windows, and great colors…. there’s just a lot of great about this place.
Planning began immediately in December; light interior work, window orders, mapping, prepping, and deconstruction in January; full building permits came early February; and now early March all framing is complete, windows arrive soon, and we anticipate all rough inspections and interior close-in for mid-April. With the interior design already sorted out and materials ready to go - coupled with the weather we’re getting blessed with - occupancy will be plenty in time for the summer season.
And with that....we're off.
Water is flowing, electricity is pumping, lights are working, floors are polished, garages are cleaned out, waterbeds are moved, furniture is being arranged for move-in, doorknobs have been adjusted, paint has been touched up, the view is still insane, the woodwork is still pretty incredible, the design and layout are awesome, trailers are hooked up to their vans and trucks and moved off the property, and final inspections are underway. Time for the grass to grow, and for this home to grow gracefully into its space.
Beer is in the fridge, too.
Awesome. Love it.






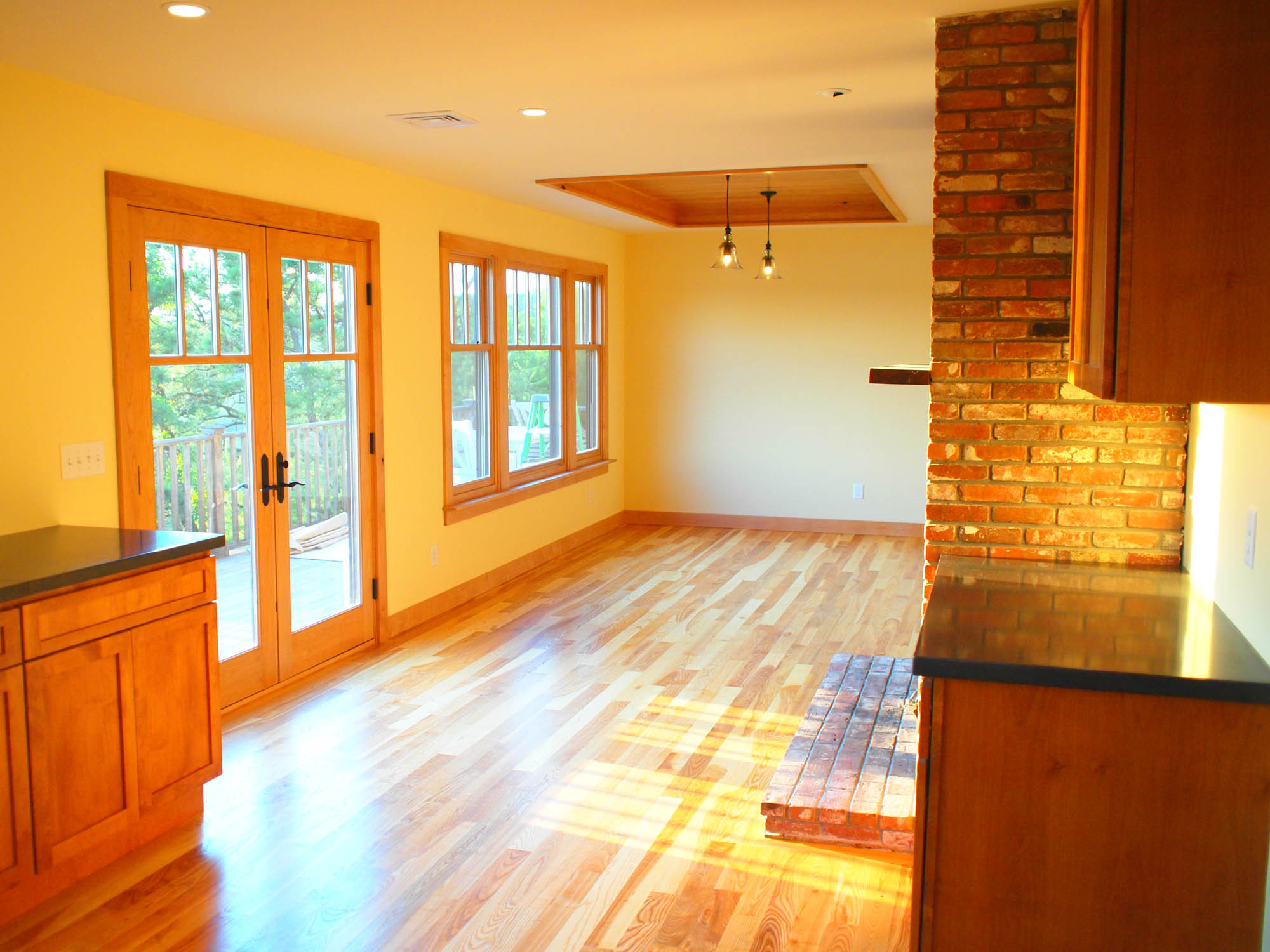







NOT spending a gazillion dollars on a tacky vanity.....
We try to use antiques in our projects for a lot of reasons; one being reduce, reuse, recycle. But it’s also a super smart economical move to look for antiques to us as vanities and built-ins when you can. The company that supplied the kitchen cabinets offered us a bathroom vanity as part of the package…for $600, not including hardware. No way.
The best antique shop on the Cape, at least as far as I think, is the one next to Captain Frosty’s in Dennis that used to be Hickley’s way back in the day. I shop for almost all our vanities at this place, and now they know when we arrive what we’re looking for. This vanity cost us $200. The sink cost me $10 at the Habitat For Humanity ReStore in Yarmouth. The faucet is the only piece that’s new, and I’m entirely okay with that. It took me about 30 minutes to adjust the bureau to accept the sink, and that was that. Plumbed up the faucet and sink myself, and they’re off and running.
It looks cool - way cooler than some boring normal cabinet. And this one has a story - no one knows it, but it surely has one. And what beats reusing something and making it awesome again? No cardboard to throw in the dumpster, no over-engineered hardware to mess with (not that I don’t like over-engineered hardware, because I do….), and the money goes right to the antique shop in town and not a company in China who shipped a bathroom cabinet halfway around the world for us. Keepin’ it in the family…or the town at least.




Lobster-Pot LazyBoy
Just because it’s cool…

Countertops, counterbalance,
There are a lot of choices in countertops for a home - go to any store and they’ll try to sell you, at minimum, one billion types of countertops. At least a billion. Maybe a gajillion. It’s a baffling process. Some are stone, some are manufactured stone, some are wood, some are plastic, some are laminate, some are marble, soapstone, ceasearstone….. It’s crazy, and it’s intimidating, and you’re likely not going to know the whole life-cycle story of your countertop because it’s very likely neither does the person selling it to you.
Here’s how this system usually works: You go into a store in Boston; you choose your countertop style from one of the billion they are trying to sell you; the store turns around and calls a supplier; the supplier turns around and calls the wholesaler; the wholesaler turns around and calls an overseas company; the overseas company calls a factory that’s employing laborers for one-dollar a day; those laborers are shaping stone from a quarry miles away; the laborers in the quarry are being paid even less than the laborers in the factory and working in dangerous life-threatening conditions; the stone you chose for your countertops is cut out of the ground by these laborers; it is then shipped to the factory; it’s shaped at the factory; it’s put on a truck to go to a port; it’s put on a boat to be shipped overseas; it lands in California; it’s put on a truck to be shipped across the country; it arrives at the wholesalers shop; the wholesaler sells it to the supplier; the supplier sells it to the retailer; the retailer sells it to you and subcontracts the installation and final shaping to a small local company - and then the retailer charges an installation fee that is more than we charge for three guys’ labor in a day…for an installation that takes 20 minutes. Now…you have your countertop that you chose at the little countertop store two months ago.
Here’s how our process has worked for the last few years: Goose and I would build your bathroom or kitchen or entire house; we’d take out our tape measures and a piece of leftover plywood and make a template of your future countertop space; we’d go to Goose’s garage and make your countertop ourselves in a garage about an hour away…maybe stop at The Mercantile for lunch (for Goose) and coffee (for me), then likely stop at True Value to say hi to Jimmy and pick up a few small parts we’d need - thereby keeping a larger percentage of our money in the local economy and not farming out all the work overseas; after we make your countertop in the garage, we’d return back to your house to continue building so nothing slows down; one week later we’d open the garage door, carry your countertops into a van, load the dogs into another truck so they don’t scratch your countertops, bring your countertops to the jobsite and install them. LIkely stop for more coffee on the way back too, at The Merc, again.
It’s an efficient process, and I think efficient is a word that could best be used to describe a lot of things we do. In fact, “Efficient” might actually be the only thing I retained from an economics degree. Anyway…
So that’s how we’ve always done it in the past. For those of you reading this who are in-the-know, obviously it would be difficult and very inefficient for Goose to be making countertops while in Australia right now. And given our workload this winter, it also would have been very inefficient for me to be trying to teach the newer guys how to make them while we should be working on the actual structural aspects of the home. For this reason, I searched out a new fella who helped us with our countertops this time around. Granted, I reluctantly had to spend a few evenings at the finer restaurants around Wellfleet and Truro looking at his work that had been installed in these places, but that grueling aspect of the task was well worth it. Derek Oliver is the man. Once I checked out a few of his pieces that had been installed, I then spent a morning at his shop and office with him learning his methods for templating, forming, mixing, pouring, finishing, etc, etc and comparing them to ours. As a big part of my job, making sure everything is okay from the initial concept idea through to the manufacturing of parts and then right on through to the installation is something in which I take a lot of pride. Derek makes his countertops about 95% identical to how Goose and I learned how to make them and have made them in the past, and Derek and I spent the morning discussing the incredibly-great-for-party-talk aspects of concrete countertops. Really enthralling stuff.
Dianne wanted dark countertops for her home. She had visited homes for which we’d made them, and she liked their feel and their look. Derek had a sample piece in his shop of a great charcoal color that I thought would match perfectly with the autumn cabinets, the alder trim, and the white ash flooring. One day after we installed the cabinets, Derek came out and templated the top. He drove home to Wellfleet. 13 days later, he arrived back at the house on a Tuesday morning with the finished tops loaded in the back of his old Ford, and the two of us carried them in and installed them. A little fine tuning, a little waxing-on and waxing-off, a little step-back-and-admire….and countertops are installed. Handmade, locally, and a billion times nicer then the billion other choices at your “local” countertop store.
I’m not saying we only use concrete tops however. I’ll encourage them always, but they’re not for everyone. You have to understand that a piece of granite is - after it goes through the before-mentioned steps of actually arriving in your region - fine tuned by lasers and machines before it goes in your home. And it will look that way. Concrete is a malleable product, and the countertops are made by hand - real hands, not machined hands - and there will be little curves and wanes and specks and other little characteristics that you’ll love. It’s a lot like soapstone in that it will change over time depending on how it’s used. A lot of people find this very attractive. I certainly do. If you think back to growing up, little things like running your hand over a divot in the countertop that Grandma used to cook on every night will remind you of the food, the family, the drinks, the process…the people.
Most importantly, the people.


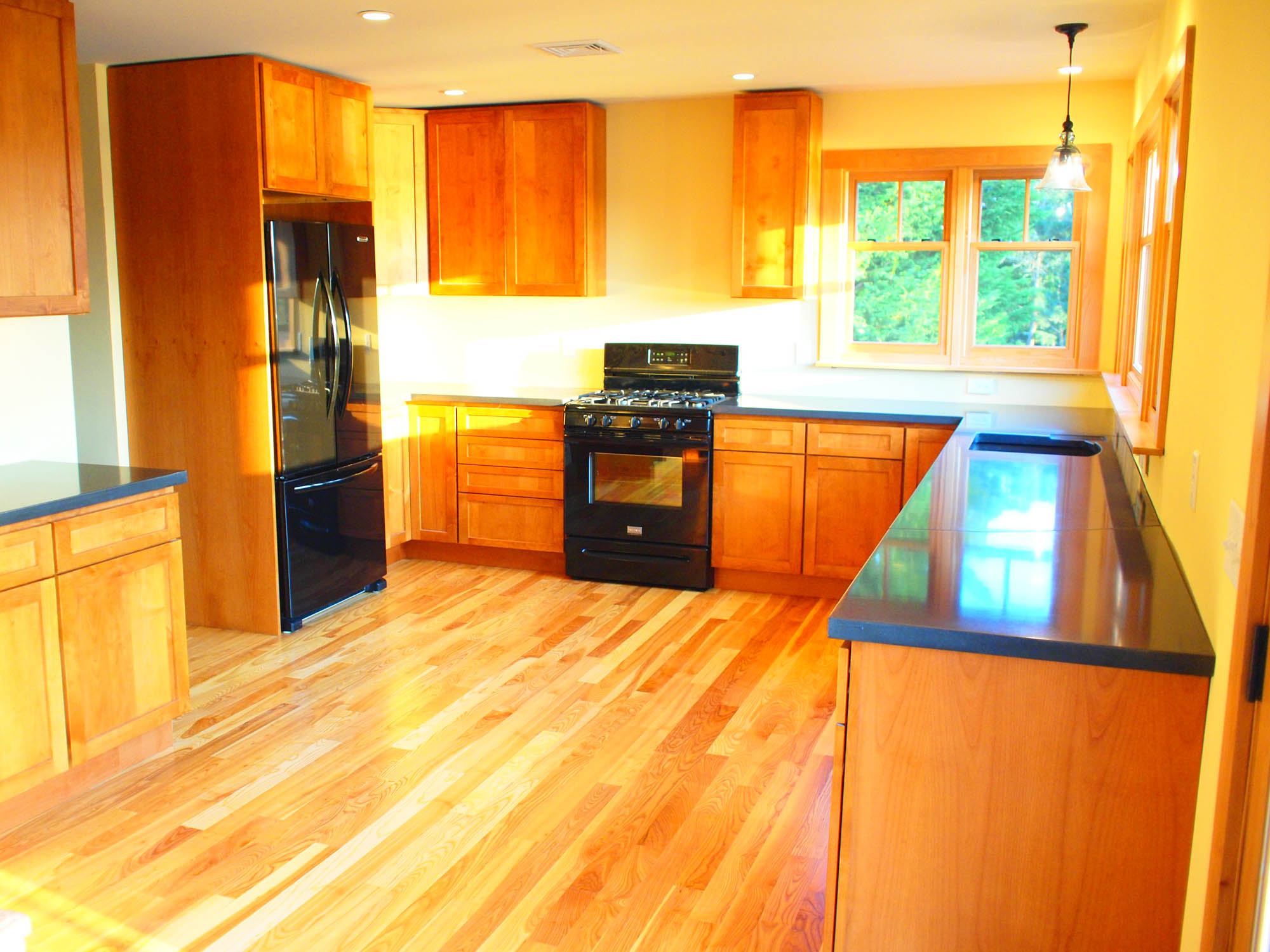



Le' Front Door...
Somewhere back amidst all of our conversations about homes and their home in particular, Dianne had mentioned to me that one of her initial dreams for this home was a red, standing-seam metal roof to cover the whole place.
Unfortunately, there wasn’t an extra $30000 in this budget for a roof alone, but I did remember that she mentioned “red” and so when it came time to choose the front door for the home, we tried to find a color that could make the place pop and tie in her thought of “red”.
Just a simple thing, but makes a big difference.


Opening a floor plan? Opening a set of plans? Planning on opening a set of open floor plans???
When we first arrived at Sheep Pond….walls, walls, walls, walls….and more walls. First part of their program: opening the floor plan. Lots of support walls later, lots of removed walls later, lots of large carrying beams later, lots of new load-points later…and we have an open floor plan with one of the best pond views in the entire town, easily.








Natural, real stone boulder walls...
With the original home sitting 3/4 of the lot’s length from the street towards to the pond, the grading ran downhill and right up to the front door. As part of the renovation process, we had to remove almost 4’ of grade-depth in order to accommodate the new foundations being above grade enough for code. In addition, water tended to run downhill from the street towards the home and then puddle up in front of the main entrance. To alleviate this issue, we’re now using natural boulder retaining walls against the grade-change to slow down the run of water and keep it from reaching the home. I’ve always been told you can’t stop water, you can only slow it down; it’s against nature to attempt to stop water anyhow. So keeping this all in mind, we’re working with SWS Services to build these walls and move water around the home and towards the pond in a natural run-off method. This will all be complemented by a natural-stone driveway that will allow rain water to move through the ground surface and into the ground below before puddling up on the Driscoll’s front yard, as happened previously.



Forks, knifes, spoons, sporks...cabinets are in.
To go along with the alder interior trim and the windows having alder interiors, we’ve chosen alder cabinets to keep the theme.

Life-cycle cost-analysis and thinking on countertops
We’re big fans of making everything that you can as opposed to buying it - when it’s possible and where budget allows, of course. Most anything made will benefit the local economy directly ten-times over; with anything bought and simply installed, the local benefit is minimal whereas the larger benefits will go to a factory overseas and the shipping channels that help it arrive in our hands after a journey around the world (spreading pollution and bad vibes all over the place…not cool). Those granite countertops may look sharp, but do you have any idae where they came from and what it took to get them from a quarry in China all the way to a kitchen in Massachusetts?
One of the biggest areas where I strongly push for a locally built item is in countertops. Concrete tops are the most versatile countertop you can imagine, or at least one of the most versatile. They’re handmade, usually by the same people building the rest of the home, and they can be built to any shape, size, form or color that you can imagine. Add in details as your heart desires; add in materials as you find them; throw in a curve here or there just to throw people a curveball - and maybe for no other reason, but that’s good enough.
In the past, we’ve made our own concrete countertops. I learned from the fellows out at Stone Soup in Northampton, MA many years back. Then a few years later Goose took the reins and really ran with that business and made some pretty incredible things of his own along the way. But now that he’s in Australia, and our capacity to make such a large top for this particular job isn’t available, we’re working with Derek Oliver out of Wellfleet, MA to make countertops for this project.
As part of the process, I’ve been out to Derek’s shop, witnessed his methods, spent a few months talking shop-and-production via email, and felt hands-on many of his past projects. And right down the type of sealer he uses, his methods are exactly the same as when we have made our own in the past. He’s a perfect fit for this job. It’s going to be amazing.

In the home stretch now....
Almost there now. Plaster is complete and coats of paint have already been applied heading into the holiday weekend. Flooring laid, cabinets installed, and we’re chugging along to the finish line in Brewster.

Let there be light...
If you don’t want to drive directly through your garage doors after a long day at school, you will need light.

Pahk the cah in the....
...garage. Complete frame with Category-C wind-load designation, i.e. an-absolute-ton-of-metal-strapping. Continuous 24’ LVL headers, blocking everywhere, Simpson HDU hold-downs in each corner so it won’t fly away. If ever the ominous 150-mph-hurricane should arrive, stand under this roof.

bang bang bang...
Just banging away…. Bedroom addition complete but we’re yet to cut through to the main house at this stage; roofline has been rearranged across the front of the home to accommodate the two additions that are being added; attached garage addition waiting in the wing on the right…

You do NOT want to fall through a septic tank...
...tank(s), plural in this case because there is also a pump-chamber tank between the home and the septic tank; this tank is hard-wired into the home, set with an alarm to go off if it ever fails, and it is the main operating system for the entire home. 99% of the time, all water and waste from a home move downhill into the tanks and then into the leach pit or drain field. It’s not as amazing as a biodigester system, or even a composting system, but it’s not a bad system. It works.
In this project, as we were excavating for the new foundations, we found the existing septic tanks to be located underneath what would eventually become the driveway to the garage addition. Not a reason to panic in and of itself because it is possible to drive over septic tanks and have no repercussions. For that to happen, the tanks need to be what’s known as H-20 septic tanks, which are traffic rated. Once we found the existing tanks, we had a few options: remove and relocate the existing tanks to somewhere else on the property; remove the existing tanks and replace with new H-20 tanks in the same location; or convert the existing tanks to H-20 via a concrete form and pour. We chose the latter option for a variety of reason, but cost, efficiency, and effectiveness all moved us towards the option of conversion of the existing tanks.
Big props to Greg Morris and GFM Excavating for their help on this. Those guys worked all day on a Saturday with me and Erik Lambton to get this thing poured and fully converted before we were able to cover it up again and continue with construction. Without this conversion, we would have had to bring in pump trucks for the new foundations, as well as offload all deliveries at the street to prevent vehicles from passing over the tanks.
Of course, we still had to move the septic lines…twice…and the wiring for the pump chamber…three times. But still.






In the beginning...
...there was a little tiny ranch home; not very well built, not very inviting, and already including some haphazard new renovation work.
But it came complete with an amazing sunset view and a waterfront location.







